Create permits to work
- Create individual PTWs or derive new ones from pre-existing PTWs
- Choose from pre-defined PTW types
- Enter exact details about the work order, time and implementation
- Specifically prepare for simultaneous on-site processes
- Link risk assessments and disclose risks associated with the activities, equipment and hazardous chemicals involved
- Define safeguards to follow before, during and after the work
- Clarify isolation and lock out/tag out (LOTO) procedures
Illustrate risks and safeguards
Regulate approval and use
- Clearly name all participants and list their responsibilities
- Use transparent status details when creating and using PTWs
- A standardized approval process makes processes safer
- Take abrupt termination of work and emergencies into account
- Generate PTWs as printable documents that can be signed and displayed openly
- Store revision-proof and consistent information in one central system
- Use the dashboard to review all PTWs in real time
- Track indicators for current and expected PTWs
- Derive updated needs for action as necessary
Check how permits to work are being used
Linked information = less effort
As a central and modular software solution, Quentic offers the advantage of being able to easily share specific information with other colleagues and departments. You can contribute to existing content and create crosslinks for your tasks with the click of a mouse. This saves time and ensures all information is accurate and up to date.
Quentic software
Combine the modules however you want!
Product
Modules & topics
- Health & Safety A system for occupational health and safety
- Hazardous Chemicals Full control of hazardous chemicals and dangerous goods
- Incidents & Observations More insights for an excellent EHSQ culture
- Online Instructions Instruct employees and external staff flexibly
- Environmental Management Track resources and costs in real time
“With its modular flexibility, networked content and centralized database management, Quentic is an outstanding integrated solution for us.”
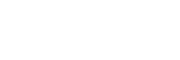
Christian Gehrke, Head of HSE Management, Business Area Equipment, GEA Group AG